Old Dominion Landfill
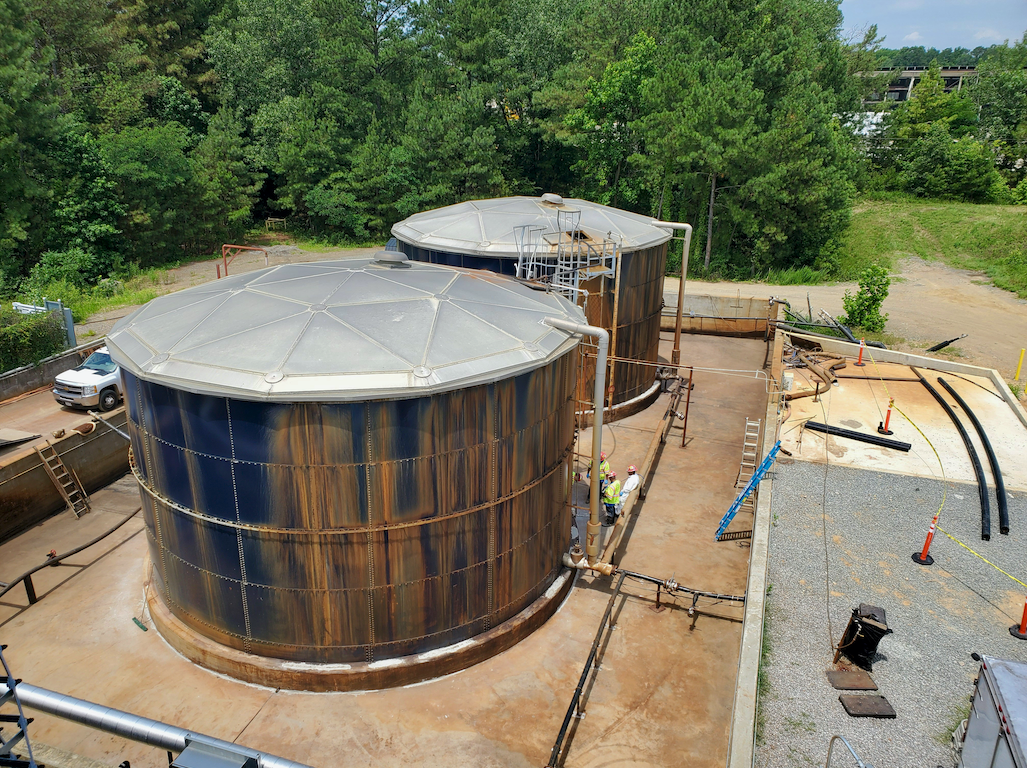
Old Dominion is a solid waste landfill located in Richmond, VA. As landfill contents degrade, a hazardous liquid called leachate is created. This liquid contains heavy metals, pathogens, inorganic chemicals, and other pollutants. Due to the high contaminant levels, leachate poses a severe environmental risk not only to public sewer systems and sewage treatment, but to streams, rivers and lakes. Therefore, landfill leachate storage tanks are essential for collecting and storing these liquid contaminants until they can be hauled off and processed.
In addition, federal law requires that secondary containment also be used to surround tanks and serve as a back-up plan in the event of spills or leaks. The secondary containment at Old Dominion Landfill is a 4000 SF walled, concrete basin surrounding 2 large carbon fiber tanks on stands, with piping and access ladders throughout. After many years of small pipe leaks, minor spills and exposure, the concrete facing of the secondary containment structure was severely caked and corroded. After completing other work at Old Dominion Landfill, Republic approached Hallaton to restore this secondary containment area.
Due to the degradation of the concrete, the intricate piping and the need to provide a watertight seal, Hallaton recommended Polyurea spray coating/liner for the job. Some benefits of using Polyurea include it being fast-setting, resistant to chemicals and abrasion, able to conform to intricate structures, UV and temperature resistant, long-lasting and ecologically friendly. It was the right product to bring life and longevity back to this essential secondary containment system.
In order to prepare the surface for application, the Hallaton crew would first need to clean and repair the concrete in order to ensure successful adherence of the Polyurea spray. All crew members wore full hazmat suits and respirators for protection throughout the entire process. The first step was to sandblast and grind the top layer of concrete around the entire secondary containment area. Once it was thoroughly cleaned and ready for the coating process, the Hallaton crew caulked all holes, cracks and pipe joints. The next step involved applying the primer. Allowing plenty of drying time in between, Hallaton then used its spray liner trailer and application system to apply 150 gallons of Black Beauty Polyurea liner to all exposed areas within the containment basin, bringing it back to life and able to perform for many more years to come.