Greensville County Reservoir
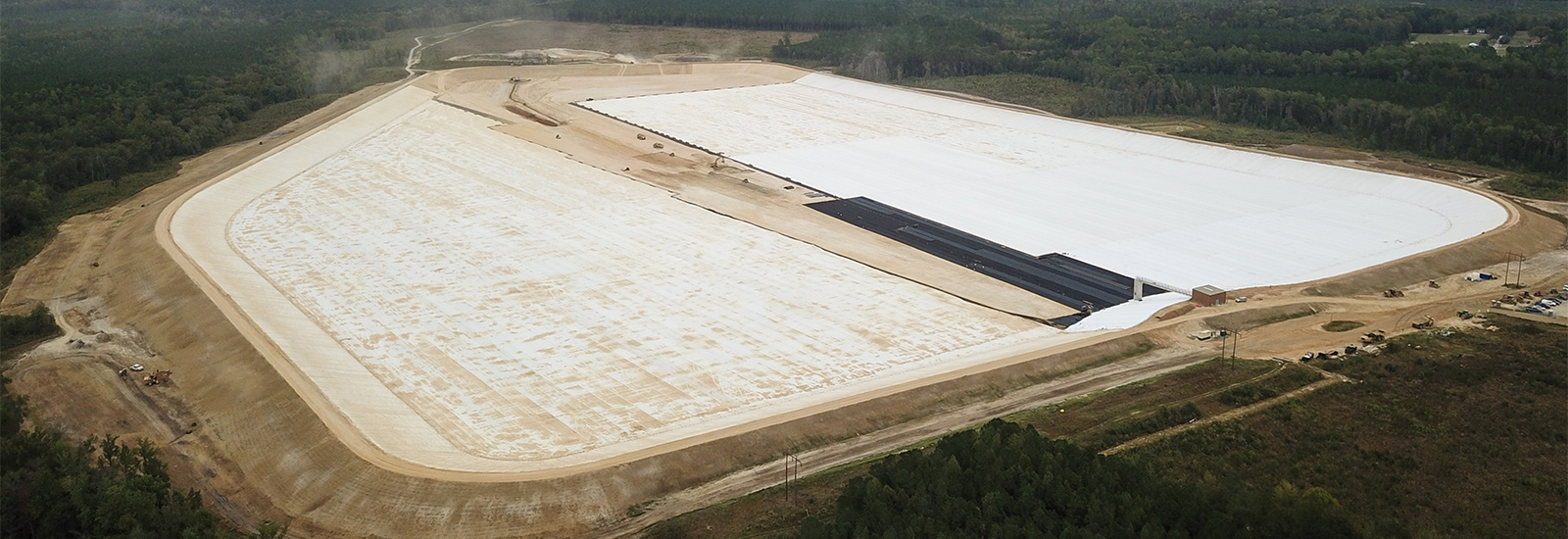
In 2017, the Greensville County Water & Sewage Authority (GCWSA) approved the construction of a new one-billion-gallon raw water storage reservoir and intermediate pump station facility in Greensville County, Virginia. The total project consisted of earth moving, construction of two large intake towers, pump installation, geomembrane installation, concrete work, and sediment & erosion controls. The raw water storage reservoir construction area consisted of 150 acres of disturbed land area.
The GCWSA awarded the contract to construct the Greensville County Reservoir to Curtis Contracting, Inc. (CCI), located in West Point, VA. CCI began construction in December 2017, moving approximately 1.7 million cubic yards of earth to form the shape of the reservoir impoundment area.
CCI also constructed the intermediate pump station, reservoir aeration, access roadways, and installation of an 18” raw waterline. Another major component of the construction of the reservoir was the installation of a geosynthetic liner system to contain the one billion gallons of raw water within the 150-acre reservoir.
CCI contracted Hallaton Environmental Linings to provide and install the reservoir’s geosynthetic liner system. CCI also asked Hallaton to provide their expertise and knowledge with regards to the designed liner system. CCI consulted with Hallaton to provide some value engineering possibilities for the proposed liner system configuration.
After CCI consulted with the owner, engineer, contractor, Hallaton and the geosynthetic manufacturer, the original liner system design was modified. The owner and engineer approved the proposed revised liner system. The value engineering liner system included the installation of a 60 mil HDPE exposed liner (smooth), textured geomembrane, a geotextile cushion layer and gas venting strips constructed of geocomposite.
Hallaton began the geosynthetic liner system installation phase in May 2018. The size of the lined area consisted of approximately 6.5 million square feet within the reservoir.
Hallaton’s field crews installed approximately 150,000 square feet of geosynthetics on a daily basis from May 2018 through November 2018. Hallaton worked continuously with CCI to ensure that a sufficient amount of prepared subgrade was available for lining installation during this time period. CCI did a fantastic job of staying out in front of Hallaton throughout the geosynthetic installation phase for the duration of this large project.
Hallaton successfully completed the installation of all layers of the liner system in November 2018. The completely lined 150-acre reservoir was tested for containment completeness by performing a leak location survey.
Solmax, the geosynthetics supplier, worked with Hallaton Environmental Linings on the construction of the Greensville County Reservoir. Over 6,500,000 square feet of Solmax’s 60 mil high density polyethylene (HDPE) smooth and textured white/black geomembrane formed the critical containment components of this exposed liner system.
The material considerations for this project needed to account for the exposed nature of the completed liner system. Solmax’s 60 mil HDPE smooth & textured white/black reflective geomembrane was an excellent fit for the construction of this one-billion-gallon exposed raw water storage reservoir.
The exposed HDPE includes a very low permeability, high chemical resistance, high temperature resistance, high tensile strength, elongation, high puncture resistance, high durability and high interface friction properties. Solmax and Hallaton worked together from the beginning to the end of this project, starting with the value engineering concepts, to the manufacturing, testing and delivery of the HDPE supplied for this project.